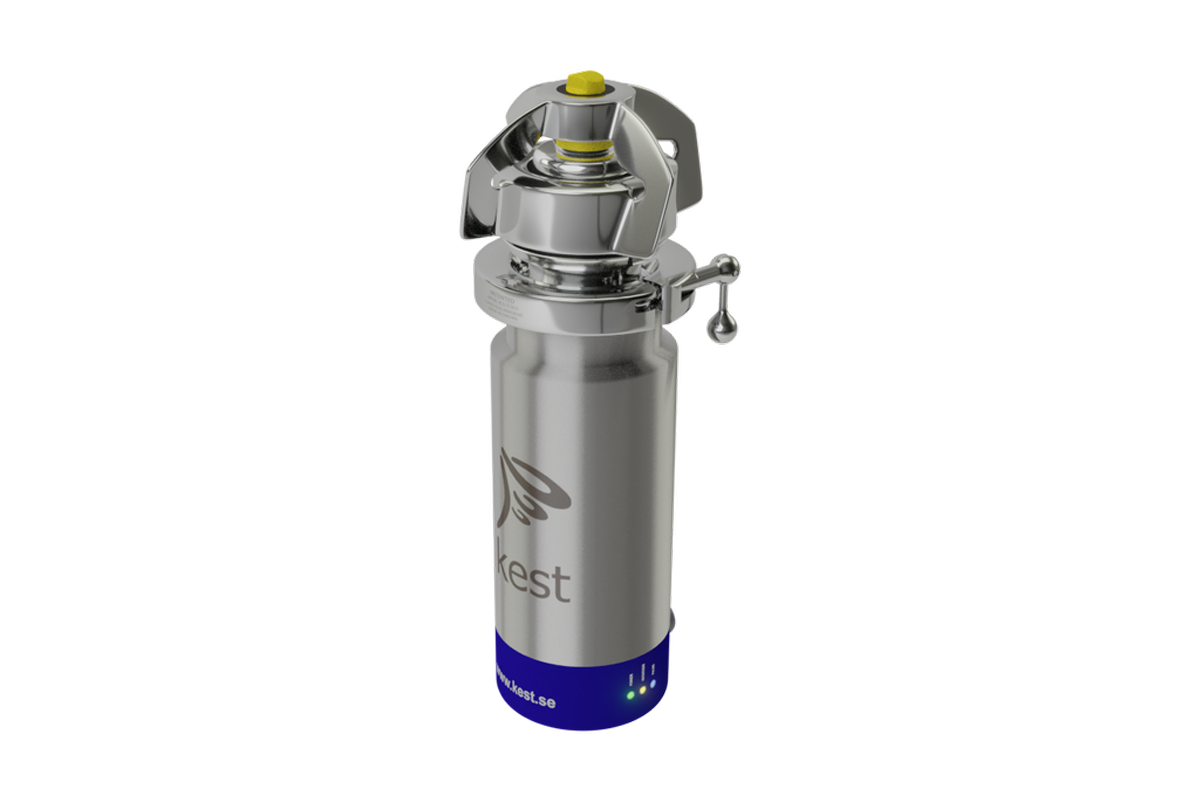
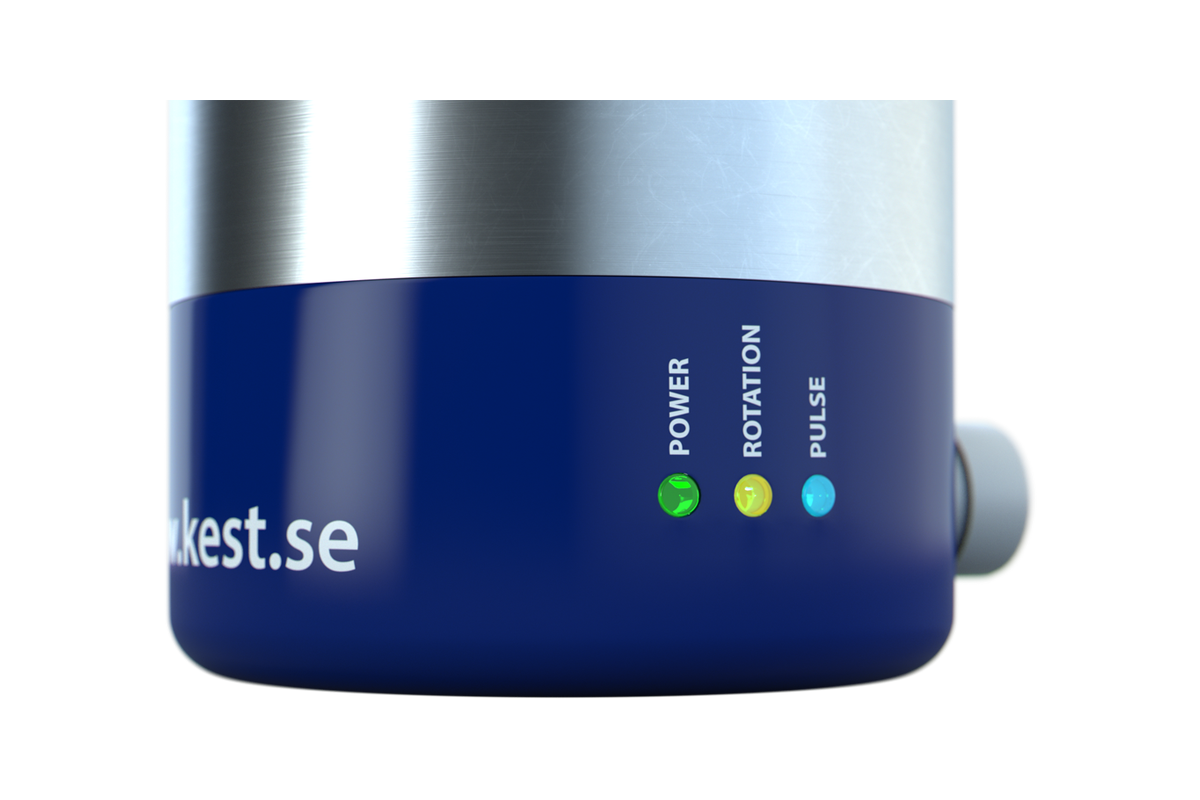
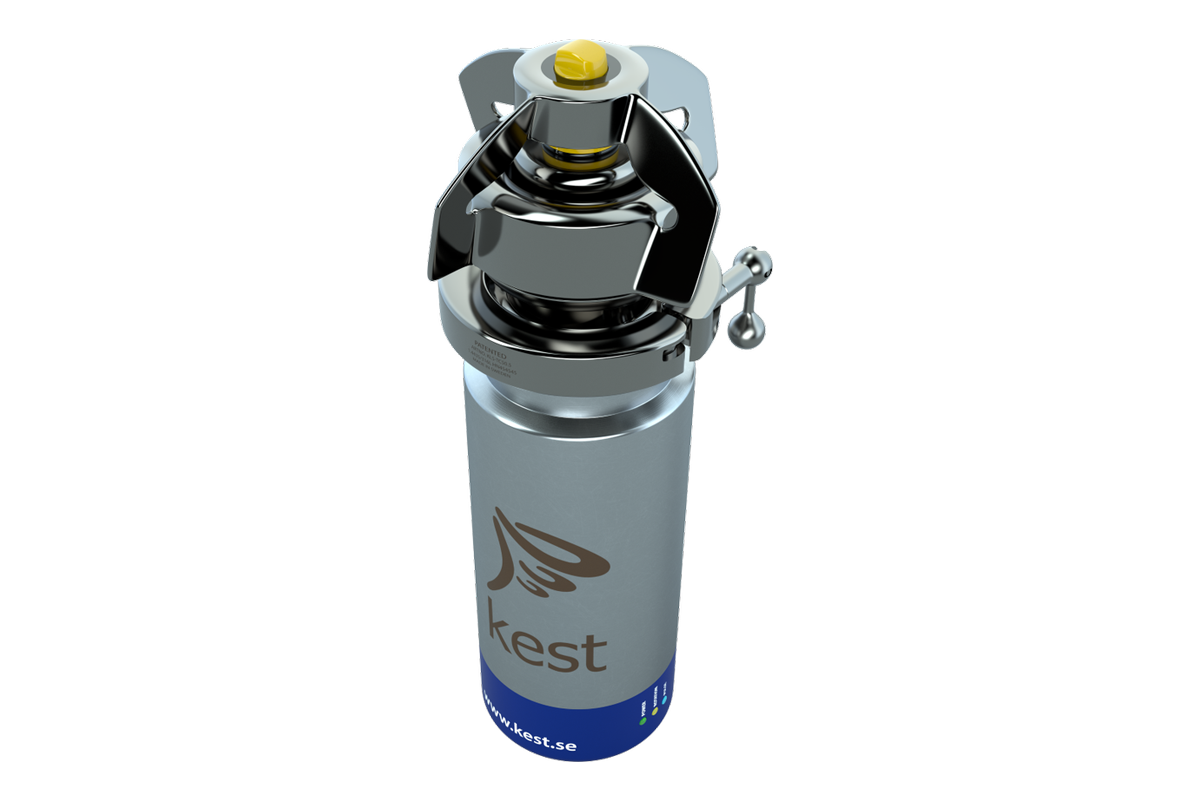

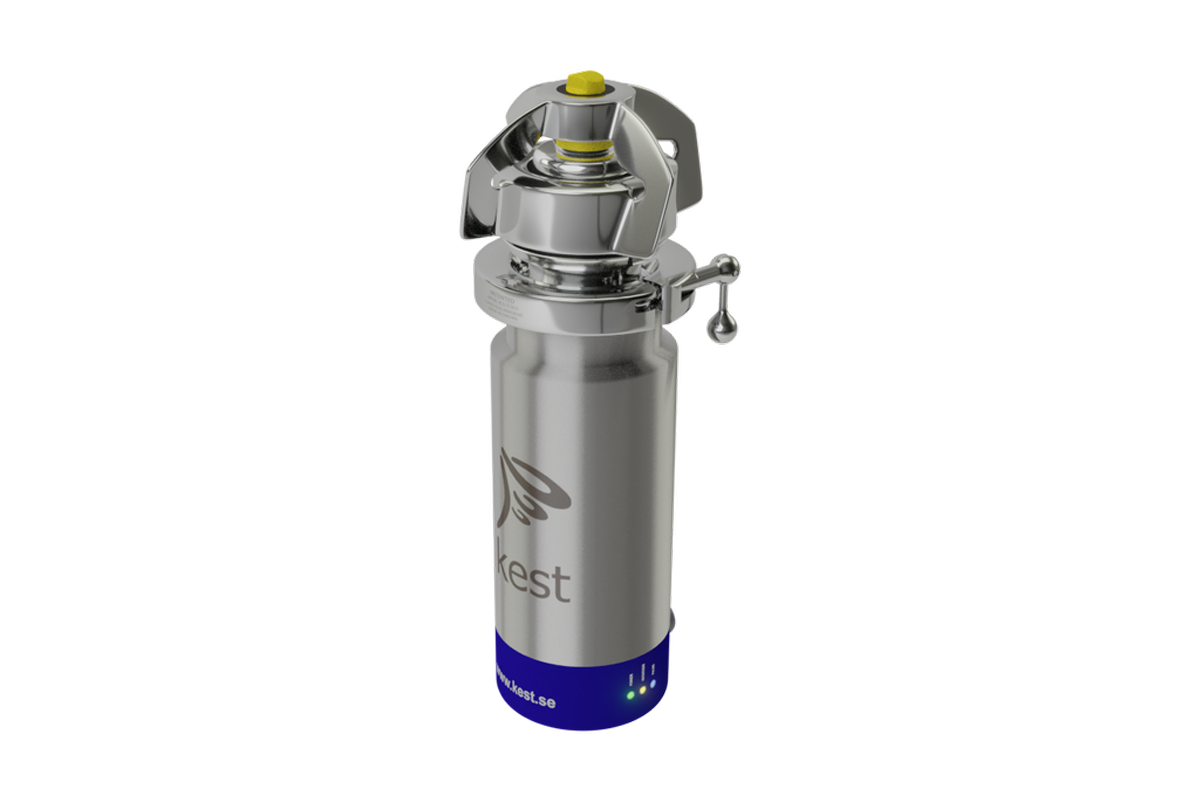
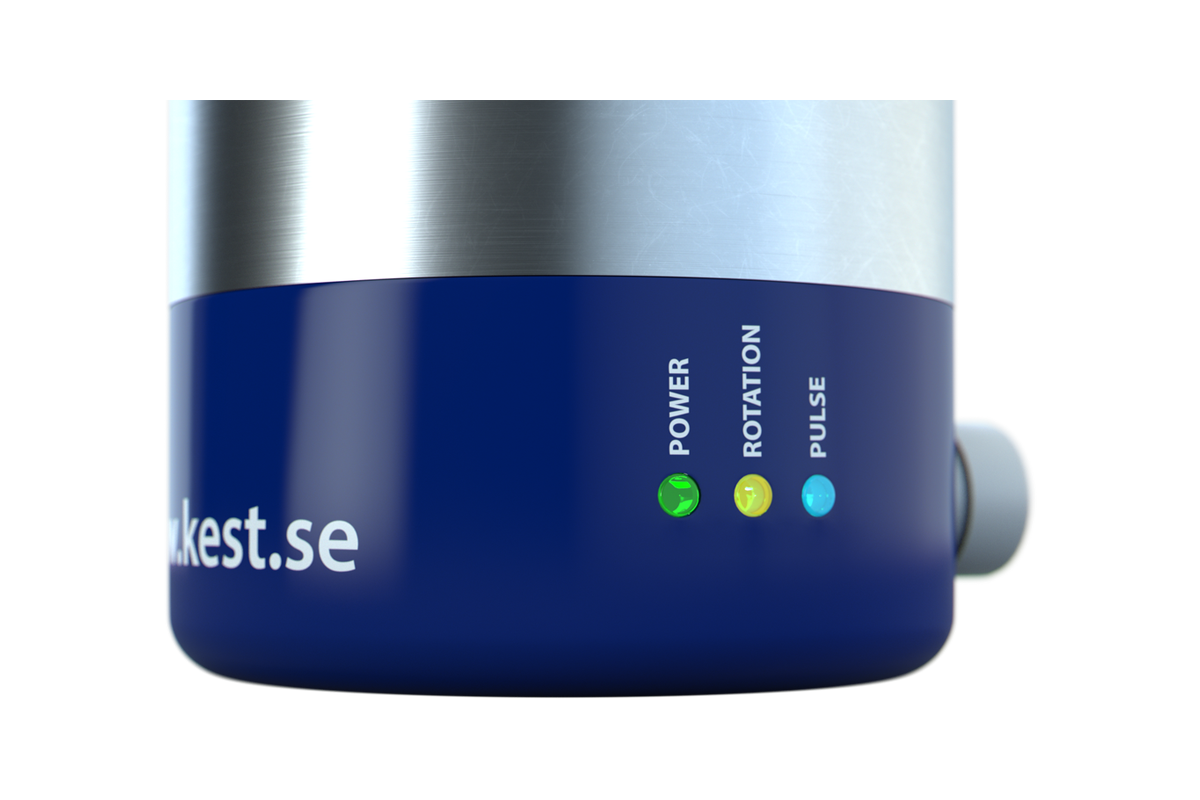
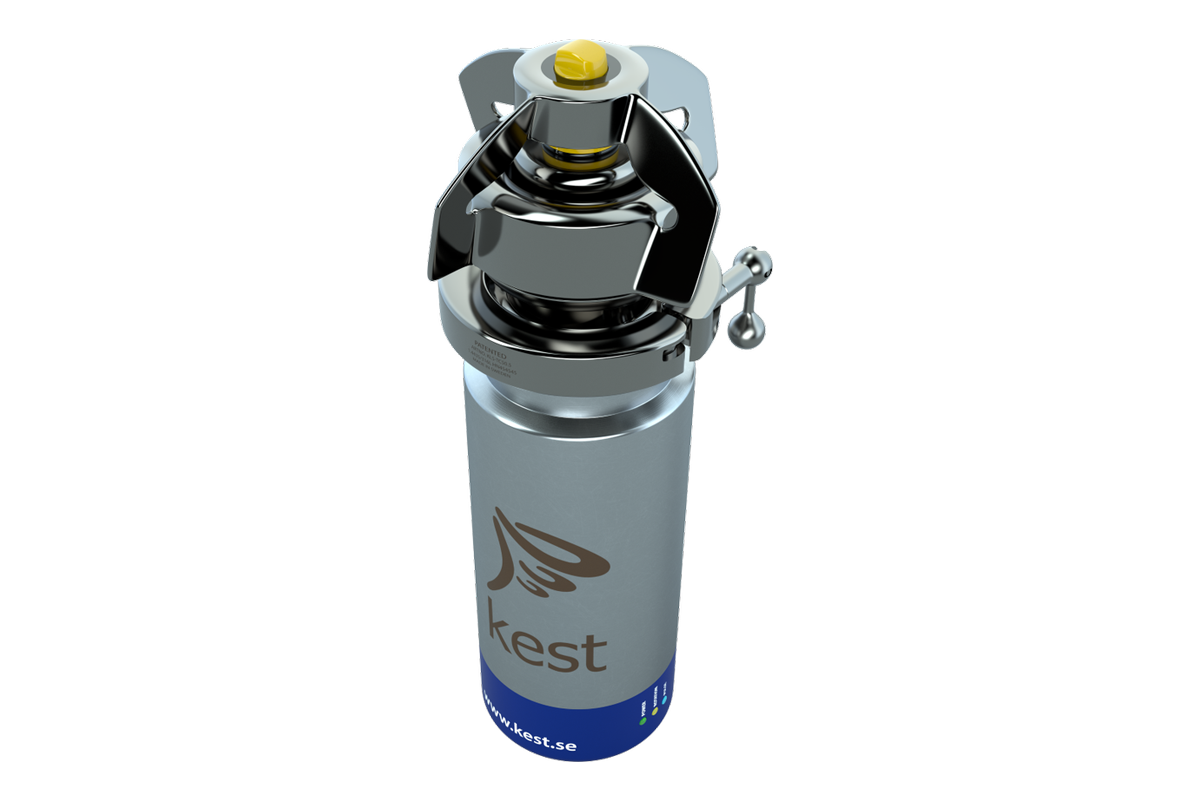

The best mixer we ever built for critical pharma and biotechnology applications.
The Kest ProFlow Mixer line is a new generation of aseptic magnetic coupled mixers. With its state of the art mixing performance and ability to mix to the last drop, it is a perfect choice for critical pharma and biotech applications. The Kest ProFlow range covers mixing volumes up to 1200 liters and is designed for CIP/SIP applications. With our advanced Speed Sensor technology, you will have a reliable process control with real time monitoring. The Drive Unit is fan-less and totally enclosed in a hygienic cover - perfectly adapted to a clean room environment.
The Kest ProFlow Mixer line is a new generation of aseptic magnetic coupled mixers. With its state of the art mixing performance and ability to mix to the last drop, it is a perfect choice for critical pharma and biotech applications. The Kest ProFlow range covers mixing volumes up to 1200 liters and is designed for CIP/SIP applications. With our advanced Speed Sensor technology, you will have a reliable process control with real time monitoring. The Drive Unit is fan-less and totally enclosed in a hygienic cover - perfectly adapted to a clean room environment.
The ProFlow DC motor has an efficiency of >95% thanks to an advanced integrated control circuit. The Pro Flow will minimize energy consumption and save both money and the environment. The unique brushless DC motor eliminates the need for a frequency converter to control the motor speed. The Kest ProFlow range can be customised to perfectly fit your needs. We offer a wide range of materials and retrofit options, please contact your reseller for a quote.
Kest has developed several product lines for various mixing applications and clean room needs. The KM product line was developed for a large volume range and the Rapid Motion (RM) line for medium shear force generation. See separate data sheets on the other product lines in the Kest Mixer family or contact your reseller for more information. The Kest ProFlow Mixer is a magnetically coupled mixer containing 4 modules, Mixing head, Male Post, Tank plate and Drive Unit.
To secure the integrity of the tank, the tank plate is welded into the tank, the mixing head and drive unit are coupledthrough the wall of the tank plate with magnetic forces. Welding tools and a welding guideline is available for easy and safe installation of the tank plate. To select the appropriate model, use the selection guide in this datasheet. For complex mixing applications contact your reseller for consultation. The Power and Logic box contains the logic unit safely mounted in a cabinet. The box comes in sizes 20/70 and 70/120, the smaller units have the logic integrated in the drive unit.
After years of experience developing mixers this mixer will deliver a perfect mixing result over and over again.
The robust bearing combination of Zirconium and Sic and the fine-tuned geometry, ensures no particle generation.
The advanced motor boosts an impressive energy efficiency of >95%. While saving money, it also helps to reduce your carbon footprint significantly and due to low heat generation there is no need for compensating cooling - you can call it - Green Mixing.
The magnetic coupling between the mixing head and drive unit ensures total integrity of the tank. All tank plates are FEM analyzed according to PED & ASME
Due to the design of the drive unit it is extremely silent during operation enhancing the environment for the operators.
The wings fixed position close to the tank bottom and the possibility to run the mixer during emptying of the tank, ensures full product recovery.
The drive unit does not contain any fans that will interfere with your laminar air flow. It is totally capsuled in a smooth hygienic cover that that is easy to keep clean.
Thanks to the advanced drive unit, the energy is converted to rotation speed and a minimum result in heat. This prevents that heat is transferred into your application.
Thanks to the advanced drive unit, the energy is converted to rotation speed and a minimum result in heat. This prevents that heat is transferred into your application.
The low weight of the drive unit and our patented Kest-Lock connection ensures quick disconnection from the tank plate during maintenance.
Mixer head | Male post | Tank plate | ||
---|---|---|---|---|
Material grade | EN 1.4435/ASTM 316L, Silicone carbide (SiC) | Zirconium Oxide (ZrO2) | EN 1.4435/ASTM 316L | |
Material requirement | EN 10 272/10028-7, A479/A240 or SA479 SA240 | |||
Documentation | Heat Certificate 3.1 acc. to EN 10 204 | |||
Surface finish | Ra≤0.5 μm on surfaces in product contact, Mixer Head manually polished + electro polished | |||
Design temperature | [0°C to +150°C] [+32°F to +302°F] | |||
Operating temperature | [0°C to +135°C] [+32°F to +275°F] | |||
Design pressure | [-1 bar(g) to + 7 bar(g)] [-14.5 psi to +101.5 psi] | |||
pH range | 1 to 14 | |||
Marking | Head and Bearing is marked with ID No. Tank plate is marked with material grade and heat number | |||
Packing | Each item is sealed in vacuum plastic bag, labelled with article code and packed in a box | |||
Male bearing sealing | EPDM, Silicone or Kalrez, approved acc. FDA regulation CFR 177.2600, USP Class VI | |||
Quality assurance | Each product is controlled and tested acc. to Kest Technology quality assurance system |
BPS SKU | Product Description | KEST Code |
---|---|---|
BP702020-128 | Mixer Head for KM-0/3, material EN 1.4435/ASTM 316L, Surface finish Ra<0.5µm, Electro polished | KM-MH0/3A-2-SiC-EP |
BP702020-129 | Male Bearing for KM-0/3 and KM-3/7, material ZrO2, with SS thread, Dia 12 mm | KM-MB12-Zr |
BP702020-130 | Tank Plate for KM-0/3, material EN 1.4435/ASTM 316L, Surface finish Ra<0,5µm | KM-TP0/3A-2 |
BP702020-131 | Welding Tool Kest Mixer KM 0/3 | KM-TP-WT0/3-6 |
BP702020-132 | Drive Unit for ProFlow 0/3, DC with SS cover and Speed Sensor | KMPF-DU0/3A-0 |
BP702020-133 | Multicable, 1 unit equals 1 meter | |
BP702020-134 | Mixer Head for KM-3/7, material EN 1.4435/ASTM 316L, Surface finish Ra<0.5µm, Electro polished | KM-MH3/7A-2-SiC-EP |
BP702020-135 | Male Bearing for KM-0/3 and KM-3/7, material ZrO2, with SS thread, Dia 12 mm | KM-MB12-Zr |
BP702020-136 | Tank Plate for KM-3/7, material EN 1.4435/ASTM 316L, Surface finish Ra<0,5µm | KM-TP3/7A-2 |
BP702020-137 | Welding Tool Kest Mixer KM 3/7 | KM-TP-WT3/7-6 |
BP702020-138 | Drive Unit for ProFlow 3/7, DC, Gear Box, SS cover and Speed Sensor | KMPF-DU3/7A-2 |
BP702020-139 | Multicable, price per meter | |
BP702020-140 | Mixer Head for KM-7/20, material EN 1.4435/ASTM 316L, Surface finish Ra<0.5µm, Electro polished | KM-MH7/20A-2-SiC-16-EP |
BP702020-141 | Male Bearing for KM-7/20, material ZrO2, with SS thread, Dia 16 mm | KM-MB16-Zr |
BP702020-142 | Tank Plate for KM-7/20, material EN 1.4435/ASTM 316L, Surface finish Ra<0,5µm | KM-TP7/20A-2 |
BP702020-143 | Welding Tool Kest Mixer KM 7/20 & KM 20/70 | KM-TP-WT7/20_20/70-6 |
BP702020-144 | Drive Unit for ProFlow 7/20, DC, Gear Box, SS cover and speedsensor | KMPF-DU7/20A-2 |
BP702020-145 | Multicable, price per meter | |
BP702020-146 | Mixer Head for KM-20/70, material EN 1.4435/ASTM 316L, Surface finish Ra<0.5µm, Electro polished | KM-MH20/70A-2-SiC-EP |
BP702020-147 | Male Bearing for KM-20/70, KM-70/120 and KM-120/230, material ZrO2, with SS thread, Dia 20 mm | KM-MB20-Zr |
BP702020-148 | Tank Plate for KM-20/70, material EN 1.4435/ASTM 316L, Surface finish Ra<0,5µm | KM-TP20/70A-2 |
BP702020-149 | Welding Tool Kest Mixer KM 7/20 & KM 20/70 | KM-TP-WT7/20_20/70-6 |
BP702020-150 | Drive Unit for ProFlow 20/70, DC, Gear Box, SS cover and Speed Sensor, Power & Logic box | KMPF-DU20/70A-2 |
BP702020-151 | Multicable, price per meter | |
BP702020-152 | Mixer Head for KM-70/120, material EN 1.4435/ASTM 316L, Surface finish Ra<0,5µm, Electro polished | KM-MH70/120A-2-SiC-EP |
BP702020-153 | Male Bearing for KM-20/70, KM-70/120 and KM-120/230, material ZrO2, with SS thread, Dia 20 mm | KM-MB20-Zr |
BP702020-154 | Tank Plate for KM-70/120, material EN 1.4435/ASTM 316L, Surface finish Ra<0,5µm | KM-TP70/120A-2-TC77 |
BP702020-155 | Welding Tool Kest Mixer KM 70/120 | KM-TP-WT70/120-6 |
BP702020-156 | Drive Unit for ProFlow 70/120, DC, Gear Box, SS cover and Speed Sensor, Power & Logic box | KMPF-DU70/120A-2 |
BP702020-157 | Multicable, price per meter |